|
Dieses Montageboard galt es zu ersetzen und so anzufertigen,
dass ein Linn Akito Tonarm montiert werden kann. Es handelt sich hier
um das originale Thorensboard von oben... |
|
|
|
... von unten... |
|
|
|
...von der einen Seite... |
|
|
|
...und von der anderen Seite. |
|
|
|
Hier der Linn Akito Tonarmsockel. |
|
|
|
Da ich keine Schablone hatte, musste ich mir selbst eine
herstellen. Zuerst habe ich den Sockel eingescannt und versucht das
Ganze auszudrucken... aber irgendwie hat die Größe nie richtig
hingehauen... trotz Anpassung. Daher habe ich einfach ein Papier genommen
und einen guten alten Bleistift und eine Andruckzeichnung angefertigt...
die hat richtig gut gepaßt zum Anzeichnen :-) |
|
|
|
So sah das ganze nach dem Fräsen aus. Ich habe zwei
rohe Boards gefräst um noch ein Ersatzboard zu haben, falls etwas
schief geht... und es ist etwas schief gegangen... das Ergebnis kann
man ganz unten sehen. Diese beiden rohen Boards habe ich dann noch ausgeschnitten
und die nachfolgenden Arbeiten wurden mit groben Feilen bis hin zur
Schlüsselfeile erledigt, mit einem Endschliff mit 400'er Schleifpapier. |
|
|
|
Hier kann man das Anzeichnen des Bohrlochs für den
Tonarm sehen. Ich habe aus einem Stück MDF mir das Anreißwerkzeug
erstellt. Vorher wurde alles genau abgemessen, angekörnt und dann
ganz genau gebohrt, und die beiden Bohrer durchgesteckt. In das Lager
habe ich einen 10 mm Bohrer gesteckt. Auf dem Board habe ich eine Markierung
für die Mitte angebracht, auf dieser Markierung musste sich der
kleine Bohrer befinden. Der Abstand von der Lagermitte zum Tonarmmittelpunkt
beträgt 211 mm beim Akito. |
|
|
|
Das rohe Tonarmboard von oben. Das Loch für den Sockel
des Tonarms ist hier schon gebohrt worden. |
|
|
|
Das rohe Tonarmboard von unten. Man kann am Rand sehr schön
die Abdeckung für den Spalt zwischen Board und Blende erkennen.
Ich habe für die Abdeckung eine Breite von 11 mm gewählt.
Der Tonarmmontagesockel liegt auch noch zum Teil auf diesem Rand auf.
Wenn ich das Board ohne diesen Rand angefertigt hätte, wäre
dieser Sockel an drei Seiten übergestanden, was auch nicht unbedingt
schön aussieht.
Man sieht auch oben deren zwei und unten eine, also insgesamt drei
Auflageflächen. Dort hat später das Board Kontakt mit der
Subchassisplatte. Die Auflageflächen sind größer als
bei dem originalen Plastikboard. Das musste so sein, da es sich um
MDF handelt, das leider nicht so feste wie Plastik ist. Beim originalen
Board werden die Befestigungs-schrauben von oben in das Subchassis
reingeschraubt und sind damit sichtbar. Bei meiner Boardversion erfolgt
die Montage von unten. Es werden die Schrauben von der Sub-chassisplatte
in das Board geschraubt, von außen unsichtbar. Das sieht auf
jeden Fall auch besser aus.
Um den Tonarmmontagesockel bestmöglich mit dem Board zu verschrauben,
habe ich mich für M 5 Schrauben aus Edelstahl mit möglichst
breitem Kopf entschieden. Dadurch das MDF unter punktueller Belastung
recht schnell nachgibt, kann ich diesem Nachgeben durch einem möglichst
breiten Schraubenkopf (große Auflagefläche) entgegenwirken.
Damit die hohen Schraubenköpfe keinen Kontakt mit dem Subchassisboden
erhalten, mussten diese um ca. 2 mm abgefeilt werden. Unter den Schrauben
habe ich noch ein Scheibe und eine Sprungscheibe gelegt.
|
|
|
|
Seitenansicht von vorne... beim fertigen Board habe ich
das Material noch etwas gleichmäßiger bearbeitet. Man kann
hier die ca. 5 mm tiefe Materialwegnahme sehr schon erkennen. Diese
wird später mit zwei jeweils 2 mm dicken Bitumenmatten aufgefüllt... |
|
|
|
...Seitenansicht von hinten... |
|
|
|
... unten von der langen Seite... |
|
|
|
... ganz rechts kann man hier die Schablone sehen, mit
der ich die Bitumenmatten angezeichnet habe. Daneben kann man beide
2 mm starken Bitumenmatten erkennen, mit denen die Materialwegnahme
wieder aufgefüllt wird. |
|
|
|
Hier das fertige Board von der langen Seite gesehen. Bei
genauen hinsehen kann man Dicke der beiden Bitumenmatten erkennen. |
|
|
|
Das fertige Board von unten... |
|
|
|
... und das fertige Board von oben... damit man etwas
erkennen kann, musste ich das Bild ziemlich aufhellen, daher sieht das
Board so grau aus... es ist eigentlich schön schwarz und leicht
glänzend durch das wachsen und polieren :-) |
|
|
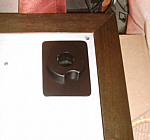 |
Hier das Tonarmmontageboard auf dem TD160. Für das
Board habe ich ca. 4 Abende, mit jeweils 2,5 Stunden Zeit benötigt.
Bis man Lösungen für z.B. das Anfertigen der Schablonen gefunden
hat, vergeht hat die Zeit wie nichts. |
|
|
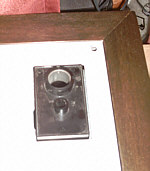 |
... und hier das originale Montageboard. Man kann den
häßlichen Spalt zwischen Blende und Board ganz gut erkennen.
Normalerweise ist noch eine silberne Blende auf dem Board befestigt,
damit wäre der Spalt noch deutlicher zu erkennen. |
|
|
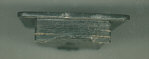 |
Und wie es so ist, ist die erste Version des Boards kaputt gegangen,
als ich zu lange Schrauben ohne vorzubohren reingejagt hatte... es
gab wieder mal Risse... naja... war halt die Lernphase ;-( ... und
die zweite Boardversion wurde dann im Detail noch verbessert... z.B.
wurde aus 2 mm Bitumenmattenauflage jetzt eine 4 mm Auflage ermöglicht.
|
|
|